Rammed earth construction, dating back thousands of years, has resurfaced as a shining example of eco-conscious architecture. In this blog post, we will delve into the world of rammed earth construction techniques, covering everything from the mixture ratios to the wall thickness and foundation considerations.
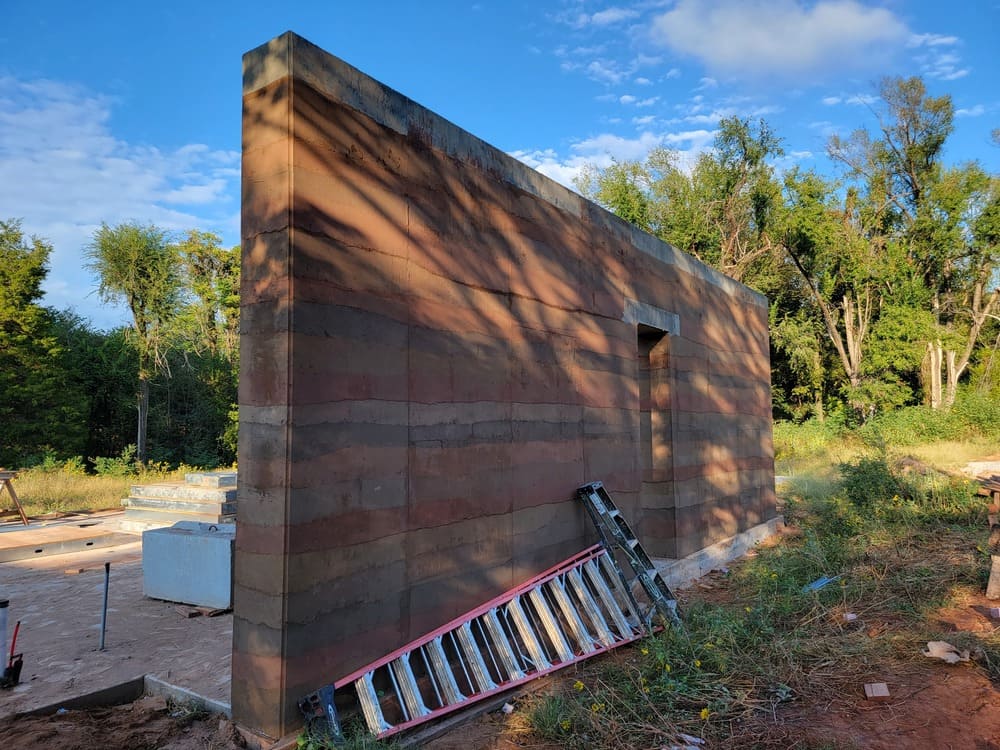
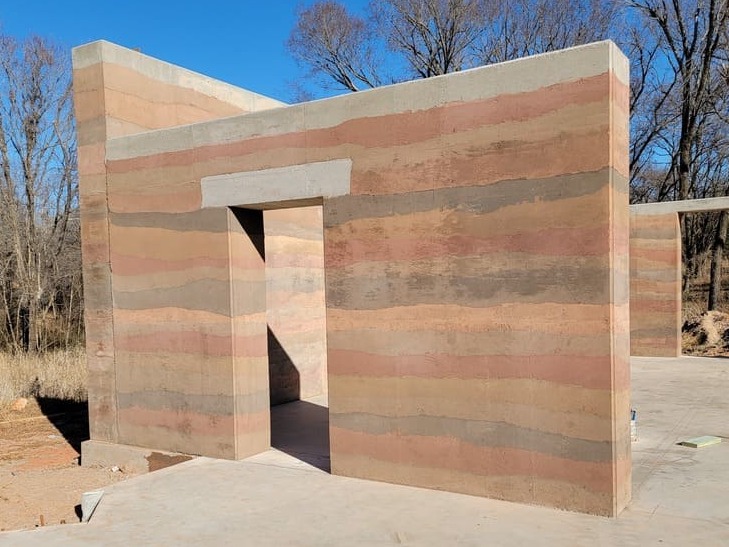
Rammed earth construction, also known as “pisé de terre” or “Tapia” in various parts of the world, has been employed by civilizations throughout history. From the Great Wall of China, the Alhambra in Spain, and the city of Shibam, Yemen rammed earth has proven its resilience and sustainability. Today, it has emerged as a prominent player in modern sustainable architecture.
Rammed Earth Mixture Ratio
The heart of any successful rammed earth construction lies in the mixture ratio. This blend of earth, often sourced locally, along with stabilizing materials, determines the strength and durability of the final product. The key elements of a good mixture ratio include:
- Earth: The primary material for rammed earth construction is the earth itself, which should have an optimal clay, silt, and sand content. Different regions offer different types of soil, each with its unique properties. Testing the soil for suitability and adjusting the mixture accordingly is essential.
- Stabilizers: Stabilizers such as cement, and lime are added to the earth to enhance its strength and reduce erosion. The ratio of stabilizer to earth varies based on the specific project and location.
- Water: Adequate moisture is crucial to facilitate compaction. The right amount of water must be added to ensure proper bonding between particles.
Rammed Earth Wall Thickness
What Is The Minimum Thickness For A Rammed Earth Wall?
In general, rammed earth walls are constructed to be at least 12 to 18 inches (30 to 45 centimeters) thick to ensure stability and structural integrity. Thicker walls may be necessary for larger or load-bearing structures. The choice of earth mix, which usually includes a blend of clay, sand, silt, and gravel, also plays a crucial role in determining wall thickness.
It’s essential to strike a balance between thickness and other considerations:
- Climate: In regions with extreme temperature variations, thicker walls offer better thermal mass and can help regulate indoor temperatures. Thinner walls may be sufficient in milder climates.
- Load-Bearing Requirements: Load-bearing walls often require greater thickness to support the weight of the structure.
- Aesthetics: The architect’s vision also plays a role. Some designs may call for thicker walls as a stylistic element.
Rammed Earth Foundation
A solid foundation is the bedrock of any building, and rammed earth construction is no exception. Building a proper foundation for a rammed earth structure involves several steps:
- Site Preparation: Clear the construction area of vegetation, rocks, and debris. Excavate the soil to the desired depth for the foundation.
- Foundation Design: The foundation should be designed to distribute the load evenly and accommodate the specific requirements of the structure.
- Moisture Barrier: To prevent moisture from seeping into the earth walls, a moisture barrier such as plastic sheeting or a layer of rammed earth with added stabilizers can be applied.
- Drainage: Proper drainage is essential to ensure that water does not accumulate around the foundation, which could lead to erosion and structural issues.
Does Rammed Earth Need Concrete Foundation?
Whether or not rammed earth construction needs a concrete foundation depends on several factors, including the local soil conditions, climate, and intended use of the structure. In some cases, rammed earth buildings may require a concrete or stone foundation to provide stability and prevent moisture infiltration. Nevertheless, modern engineering and construction practices have evolved to include various foundation options that minimize the use of concrete, such as rubble trench foundations or reinforced concrete footings only at load-bearing points.
Rammed Earth Formwork
While the mixture ratio, wall thickness, and foundation are integral to rammed earth construction, the formwork used during the building process plays a significant role in shaping the final structure. Formwork is essentially the mold or framework that holds the rammed earth mixture in place until it has solidified. There are several types of rammed earth formwork, each with its unique advantages and considerations.
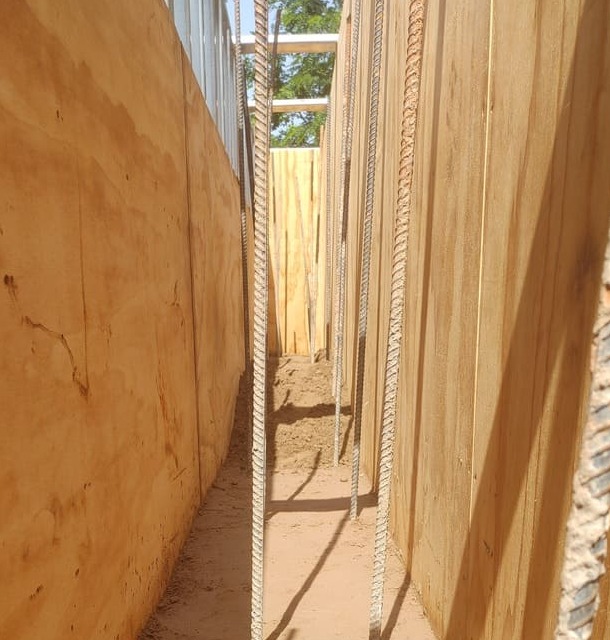
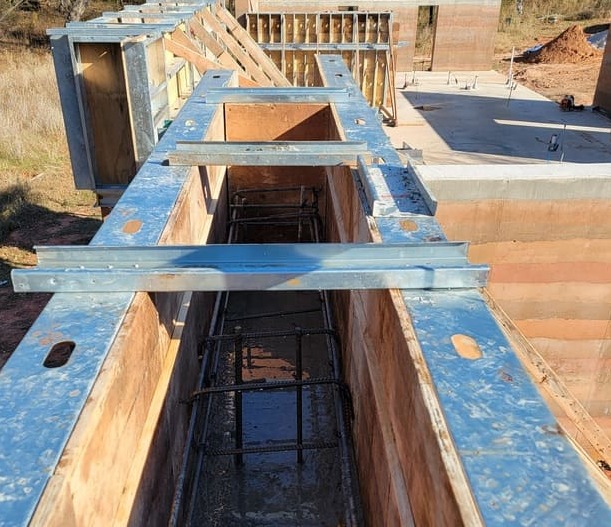
a. Plywood Formwork
Plywood formwork is one of the most common and versatile options for rammed earth construction. It consists of sheets of plywood that are assembled to create the desired shape of the wall. Here’s why plywood formwork is a popular choice:
- Flexibility: Plywood formwork allows for various wall shapes and sizes, making it suitable for both straight and curved walls.
- Reusability: Plywood can be reused for multiple projects, making it a cost-effective option over time.
- Smooth Finish: The smooth surface of plywood can result in an aesthetically pleasing, refined finish for the rammed earth walls.
b. Vertical Stack Formwork
Vertical stack formwork involves stacking horizontal layers of material on top of one another to form the walls. Each layer is compacted before the next is added. This method has its own set of advantages:
- Simplicity: Vertical stack formwork is relatively straightforward and requires minimal materials, making it accessible for DIY enthusiasts.
- Structural Strength: The method inherently creates strong, load-bearing walls due to the layer-by-layer stacking and compaction.
- Sustainable Aesthetics: The exposed layers of earth create a visually striking appearance that highlights the natural beauty of the rammed earth.
c. Slipform Formwork
Slipform formwork is a continuous casting method where a formwork structure is moved vertically upward as the rammed earth mixture is poured and compacted. This technique offers unique benefits:
- Speed: Slipform construction can be significantly faster than traditional methods, making it suitable for larger projects.
- Consistency: The continuous upward movement of the formwork ensures a consistent wall thickness and surface finish.
- Minimal Joints: Since slip-form construction is continuous, it results in fewer visible joints or seams on the finished wall.
d. Prefabricated Formwork Panels
Prefabricated formwork panels are factory-made panels designed to specific dimensions and shapes. They are transported to the construction site and assembled to create the formwork. This method is gaining popularity for several reasons:
- Precision: Prefabricated panels are manufactured with precision, ensuring uniform wall thickness and an even surface.
- Time-Efficiency: Assembly of prefabricated panels on-site is quick and efficient, reducing construction time.
- Quality Control: The controlled environment of the factory allows for better quality control, resulting in consistent and durable formwork.
Conclusion
Rammed earth construction techniques offer a remarkable blend of sustainability, durability, and aesthetic appeal. From mastering the art of mixture ratios to carefully selecting the appropriate wall thickness, foundation, and formwork, this age-old building method is experiencing a renaissance in the era of eco-conscious architecture.
If you’re inspired by the possibilities of rammed earth architecture and have a project in mind, we invite you to take the next step. Contact GLS Rammed Earth, your partner in turning your rammed earth dreams into reality. With our expertise, we’re here to guide you through every step of your rammed earth journey.